2021 Application Innovation Award Nomination: Browns Shoes: Automating Supply Chain and Operations processes
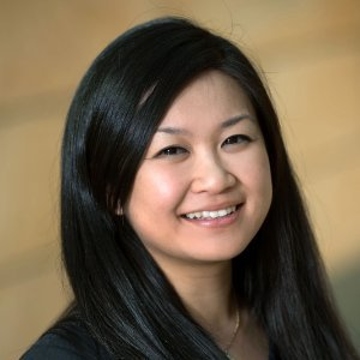
- Mark as New
- Bookmark
- Subscribe
- Mute
- Subscribe to RSS Feed
- Permalink
- Report Inappropriate Content
11-19-2021 12:00 AM
What were the underlying reasons or business implications for the need of application integrations? Describe the business and technical challenges the company was facing and how application integrations can help.
As a Canadian leading independent footwear chain, Canada-based Browns Shoes is widely acclaimed for providing a consistent, best-in-class shopping experience for fashion footwear, backed by exemplary customer service.
With high customer expectations and the company’s impressive organic growth as the backdrop, Browns Shoes was looking to accelerate its direct to consumer processes and optimize employee efficiency by leveraging data and technology.
Paramount among Browns Shoes concerns for optimizing its processes were:
- to provide employees with a thorough and efficient application that will require minimum training thus improving on-boarding of new employees, both at its distribution center and 70 retail stores,
- to ensure adherence to the company’s high standards for salability by providing specific guidelines custom to each product, and
- to identify any products with issues, missing parts (e.g. buckles, laces), or damages before shipping that would result in customer dissatisfaction or product returns.
Built on top of the SnapLogic Platform, Browns Shoes rallied to build the fully integrated – Browns Inspection App – an innovative, dynamic, user-friendly, and efficient application to address specific issues and challenges, including:
- Low employee productivity associated with the level of manual work involved in system synchronization,
- The absence of real time and reliable interaction with the order management software system, shipment services, and local databases,
- Old logic and outdated systems that were difficult to maintain and improve, and that didn’t allow introduction of new features, such as printing return labels, invoices, and shipping labels.
Describe your application innovation strategy and how you executed the strategy. Include details on how SnapLogic played a role in the strategy and execution, including Snaps and other SnapLogic products/features.
At a macro level, SnapLogic connected the dots between the order management software, local databases, multiple shipping carriers, printer servers, and legacy systems. Where the innovation is especially evident is the development of a very agile solution that is able to adapt the workflow based on each and every order placed. The application instructions are fed from an Excel spreadsheet that is maintained by non-programmers who are able to modify workflows by adding steps, comments, pictures, etc. and based on the products in the order, SnapLogic will connect the dots between the config file on one side and the Browns Inspection App on the other side. As the key backend tool, SnapLogic’s innovation provides dozens of real time application programming interfaces for product inspections and shipping at Browns Shoes’ distribution center and retail stores.
At a micro level, the Browns Inspection App replaced the legacy application which was previously used by the distribution center to clean and pack orders, communicate the status of orders with the OMS and all other applicable systems. Because the original and outdated application was written in traditional object-oriented language that made application updates and feature additions laborious, Browns Shoes built the new web application from scratch and meticulously designed customizations aligned with their application development best practices and strategic business objectives. The new software accelerates employees’ activities and enables them to conduct tasks quickly and efficiently.
The Planning Phase consisted of:
• Defining the database structures
• Creating authentication rules
• Preparing configuration files
• Determining SnapLogic’s high-level architecture
The Execution and Implementation Phase consisted of:
• Building CRUD functionality into user management
- Built the authentication mechanism
- Built the Browns Inspection App for use at the Browns Distribution Center and in 70 retail stores across Canada
- Developed logging and statistics async processes
• Testing and bug resolution
• Deployment using GitHub, the world’s most advanced development platform
To ensure enterprise-wide optimization, SnapLogic customized intelligent automation to connect the dots between data and the app. Specifically:
• By adding more nodes to Browns Shoes’ user-defined Snaplexes, SnapLogic enhanced the app’s performance: Exposed APIs are called using their ground URLs, allowing for an unlimited number of calls, and using caching feature on the ground. As a result, these APIs power Browns Shoes with data-driven results and support the company’s digital inspection objectives:
- To connect to APIs without manual coding, which decreases errors and reduces the need to have in-house programming skills
- To retrieve and process specific API data, which reduces complexity and overhead
- To reuse the connector to maintain consistency and reduce overhead
- To efficiently manage API data flow
- To execute any API call at the location closest to the data source for more efficient processing
• SnapLogic’s solution used most of the basic snaps because the endpoints were either SOAP-based or REST-based calls. Additionally, SnapLogic used calls to AWS and internal DBs.
Who was and how were they involved in building out the solution? (Please include the # of FTEs, any partners or SnapLogic professional services who were involved on the implementation)
- Browns Shoes: Alexandre Hubert, Senior Director – IT Strategy & Logistics
- Browns Shoes: Gérémy Cloutier Gill, Logistics Manager
- Browns Shoes: Joshua Frankel, Data & Integration Architect
- ⋮IWConnect: Petar Rajchinoski, Senior SnapLogic Developer
What were the business results after implementing these application integrations? Describe how your company, departments, and/or employees/customers benefit from the application integrations. Include any measurable metrics.
As a result of SnapLogic’s innovative application integrations, Browns Shoes has benefited from an extensive range of operational efficiencies.
• Employee productivity has increased exponentially as a result of the elimination of manual inspections and better directed workflow.
• Reliable and headache-free migration process from dev to prod within 5 minutes.
• The innovative solution is scalable, and the app’s flexible logic allows for fast and easy introduction of new application features.
• Control and traceability of the full inspection, packing, and shipping processes have improved dramatically, and Browns Shoes can track which employee cleaned, packed, and shipped the product, how much time each step took, and decisions made during the inspection process.
• SnapLogic’s fully dynamic, flexible inspection process detects and records product issues and has the important capability of taking real time pictures of products, assigning the appropriate issue category to anything damaged, and providing an archivable photo asset for potential future use by customer service representatives.
• Real time data synchronization and connection among all enterprise systems – OMS, Shipment, AWS, and DBs – has a positive impact on business systems, time and cost efficiencies, inventory integrity, logistics and shipping decisions, sales, time to customer, customer satisfaction and retention, and brand reputation.
• Trackable tables designed by SnapLogic provide for easy reporting by business intelligence teams to analyze data, gain actionable insights, and improve decision-making.
• Paramount to best practices, SnapLogic’s innovative application gives Browns Shoes an accurate, real-time status of every product SKU, shipment, and employee inspection activity.
SnapLogic’s innovative application integrations have delivered a wide range of supply chain benefits and best practices for Browns Shoes and its valued employees. Among them:
• Logistics analysts are driving and managing the fully dynamic application internally without assistance from the IT department by maintaining a configuration file as an entry point for SnapLogic API integrations.
• The application has given management visibility to an entirely new data set to accelerate its processes and deliver products into the hands of customers as quickly and cost efficiently as possible.
• Employee productivity has skyrocketed.
• Useful, timely feedback has been given by employees about the usability and functionality of the new app as compared to the old process.
• Every product SKU and shipment can be tracked in real time by every team (business intelligence, managers, and IT).
• Dynamic functionality allows for logistically favorable shipments to be sent directly from stores, resulting in faster deliveries to customers and lower shipping costs.
• Intuitive functionality means minimal training time, which is particularly beneficial during seasonal hiring spurts in which employees need to be productive quickly to meet escalating demand.
• Ease of use has dramatically reduced errors to near zero, expedited the speed of shipping, and ultimately enhanced the Browns Shoes customer experience.
• Special user instructions can be defined in the configuration file based on rules and conditions dynamically resolved by SnapLogic.
• The multi-language application – English, and French – opens windows of opportunity to attract and retain employees beyond those who are native English speakers.
Anything else you would like to add?
- Because SnapLogic’s application is a component-based framework, it ensures easy customization and reapplication to other business units.
- SnapLogic has leveraged data and technology with tremendous innovation and precision to manage Browns Shoes’ supply chain, ultimately boosting Browns Shoes’ reputation even higher as North America’s leading independent footwear enterprise providing a best-in-class shopping experience.
